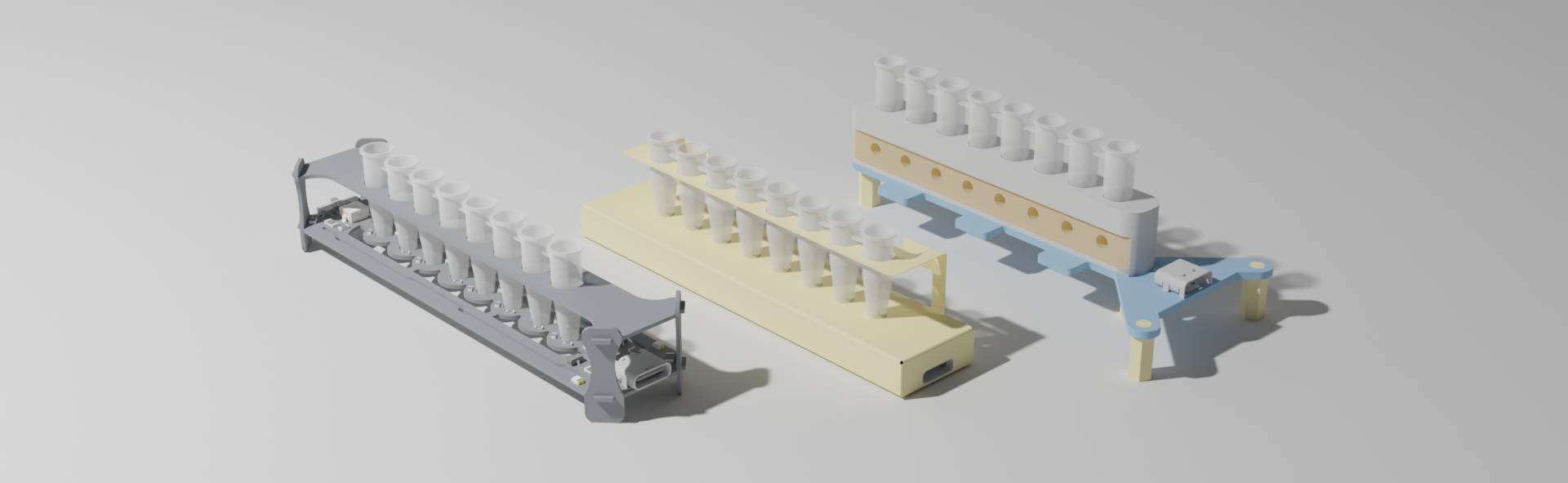
We are back! Second prototype and final iteration
First things first! We would like to apologize to everyone following and supporting the project for the lack of updates over the past year. Many changes have occurred in the professional lives of @Felipe and me (we both moved to different countries and started Master / PhD programmes), and life has been busier than expected.
But we haven't forgotten about nanoLAMP! We've worked on two new prototypes—one of which we're sharing the results here, while the next is currently in production and will be tested in the coming months. We aim to share the final results by mid-2025 and bring the project to a close.
Second prototype: Foldable flexible PCB
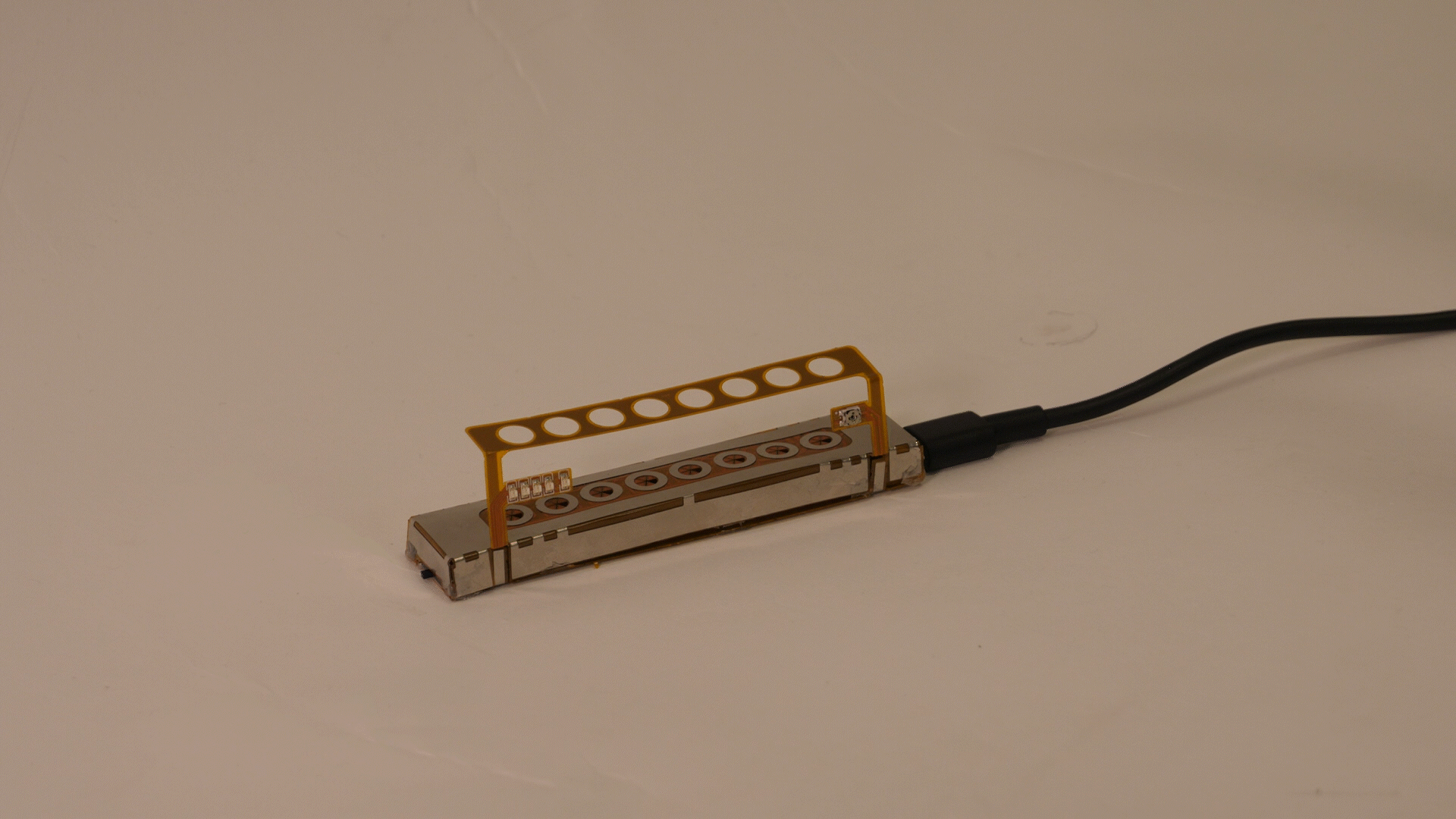
Let’s quickly recap the previous lab note. The most significant problem in the last iteration was that the heating region — the ring — was quite small compared to the total surface of the tube. This led to heat dissipation from the ring region into the rest of the tube, with the severity of the dissipation depending on the external room temperature the tube was exposed to. For example, we tested it at -4ºC in the Chilean Patagonia and the liquid reached just 37ºC out of the 63ºC we configured.
To fix this, we came up with the idea of using a foldable PCB, where the tube passes through a hole shaped like a foldable pie chart. In this way, the sectors — which are also covered by heated copper pads — fold around the tube, increasing the heating contact area.

Additionally, once the PCB is folded, it creates an inner chamber that is heated to 25ºC by internal resistors. This ensures that the bottom part of the tube is always exposed either to the 25ºC of the internal chamber or to the chosen incubation temperature (for instance, 63ºC for LAMP reactions).
The device comes as an unfolded PCB, with stainless steel protecting the outside part and strenghtening the structure after folding. Even though is a metal, the heat transmission of stainless steel is quite low (more than ten times less than alluminium or copper), which considerably reduces the heat dissipation by the case.
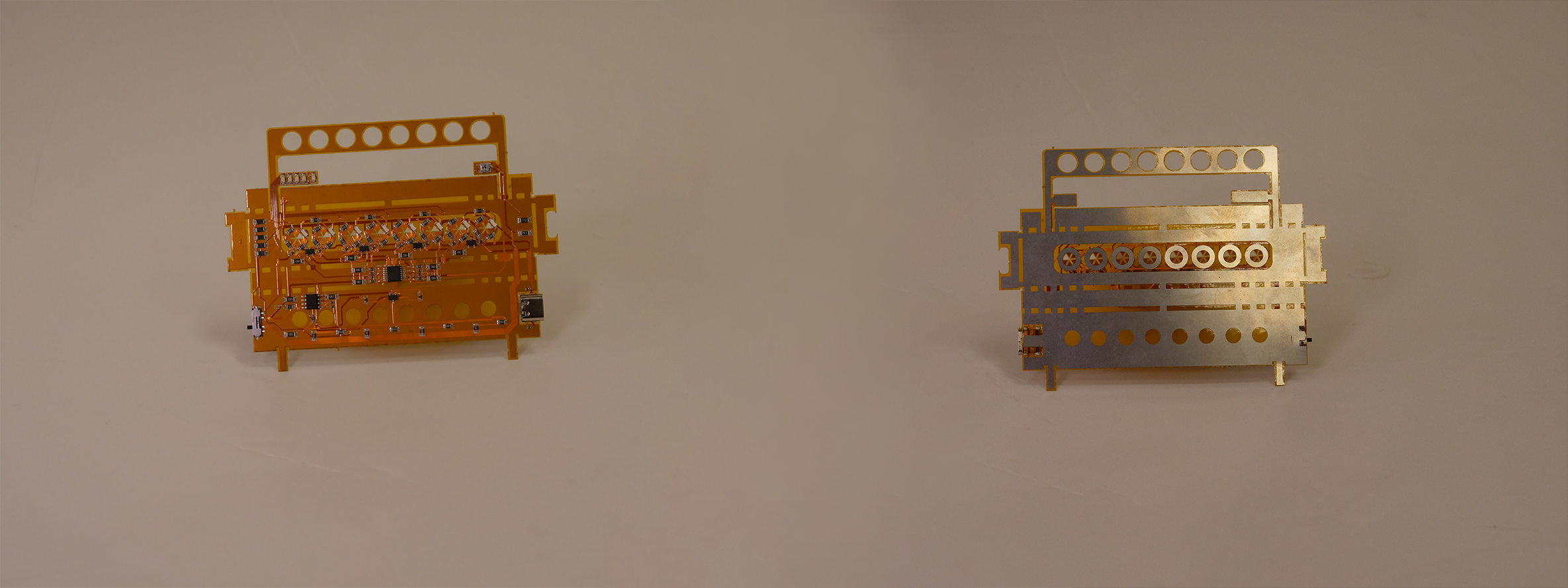
After been folded, the device looks like a little tube holder, with 4 LEDs reporting the activity of each heating segment (one per two tubes) and another one indicating the activity of the internal chamber heating.

Mechanical test
Here we found the main issues. Flexible PCBs are a tricky material when considering mechanical strength, primarily because bending can cause components to unsolder and copper paths to break. The stainless steel stiffener provided some support, but was not as stiff as a solid material; a critical point of failure was the USB connector.
USB connectors are typically recommended to be through-hole, meaning their pins extend through the PCB and get soldered on both sides, providing mechanical strength and preventing damage during repeated plugging and unplugging. However, adding through-hole pins does not allows for stainless steel stiffener beneath the PCB, as the pins extend through to the other side.
We placed the stainless steel stiffener everywhere except beneath the through-hole pins (see figure below, left side), but this left the some parts of the PCB uncovered, which at the same time were the ones that suffered more when the user plug and unplug the connector. This cause the PCB break easily on the unprotected material, affecting some of the main voltage lines and cutting power to the entire system. The second problem was keeping the case closed. Stainless steel is not as malleable as aluminum and it failed to keep the shape as stable as we needed. We tried to solder the steel pads, but the solder would not stick. In order to move on to some reaction tests, we opted for the 'simple-but-ugly' fix of using hot glue. If we were to stick with this design, a better solution would be to add exposed copper pads on the borders so the user could solder the different sides together.
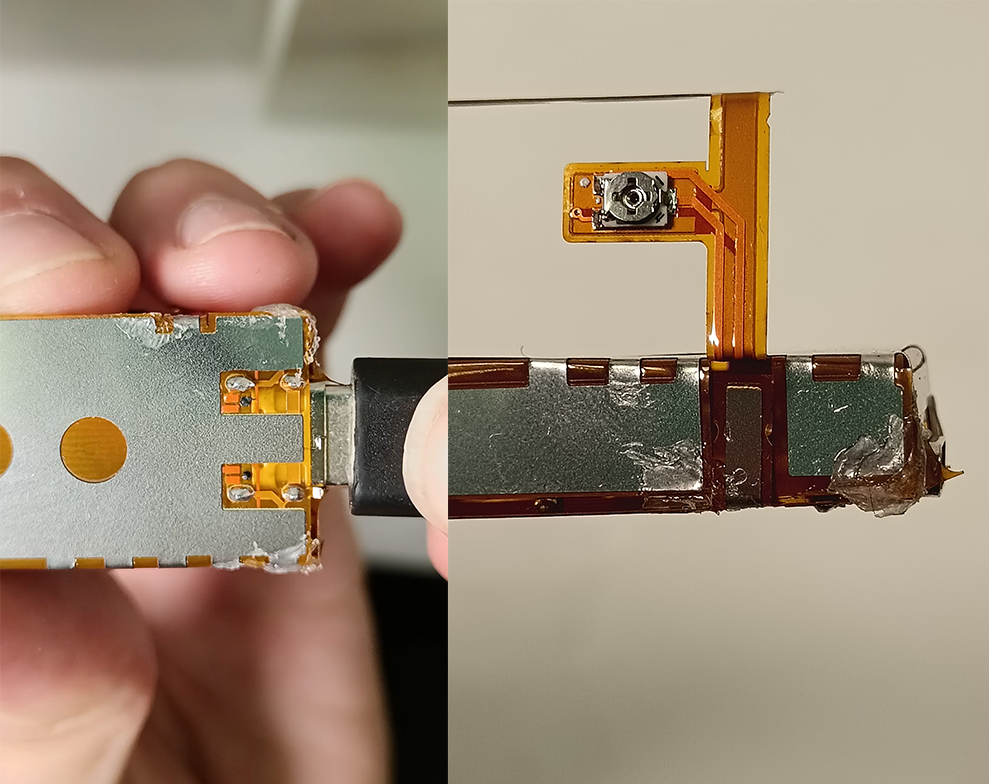
Fluorescence test During testing, we found the foldable pie chart design impractical. Instead of holding the tubes, the sectors pushed them outward, bending the flexible material when pressing the tubes in and out, and getting it damaged after a few trials.
The lateral LEDs worked, but their position on the holder affected both how the fluorescence was projected below and how the LED light illuminated the sample. As the tubes were not properly holded on position and the material was deforming, this made the whole fluorescence readout really tricky.
In this design we used the PCB material as a filter, removing the stainless steel, components and traces creating a circle right below the tubes with just the translucent PCB material ( polyimide). Overall it worked for filtering some of the blue light, but it clearly performed worse than other filters we used in the past (as the Lee Filter used in the previous version).

Heating test Finally, we tested the heating system and found two main issues:
As the tubes did not fit well and uniformly into the holder, the heating contact was unefficient.
We realized that the stainless steel case, which we hadn’t grounded, acted as a capacitive antenna. This introduced electrical interference into the analog circuit responsible for controlling the on/off temperature switching.
Is foldable electronics the final answer?
Our conclusion: Foldable electronics are not the answer, at least in the short term. Don’t get us wrong; we still believe foldable electronics have great potential for portable, easy-to-assemble hardware, and there are some great ideas we found interesting during the testing phase. Particularly they might be interesting in the future for 'hybrid' prototypes where the PCB serves both electronic and structural roles, while also offering users a fun "PCB origami" experience to assemble the product. However, to develop a reliable system, we would need to iterate several more times, which falls outside the scope of this project.
Closing up the project
At this point, our main goal is to deliver a simple, functional solution that our collaborators can begin using in fieldwork. While we are still interested in exploring new possibilities, such as puzzle PCB prototypes and foldable electronics, we believe this phase of the project—supported by our funders one year and a half ago—should come to a close with the delivery of a final working prototype.

So for this final prototype, we want to keep it simple. The new design is made of a standard, 2-layer PCB with digital electronics, that will allow us to change the code and test different configurations.
The tube holder will be 3D-printed in aluminum, solution we already tested in other hardware designs. This helps with the heat distribution, provide a robust mechanical fitting, and remains relatively affordable at approximately $10 per tube holder.
The aluminum holder will be heated from the bottom, with LEDs positioned right below to illuminate the tubes. For checking the fluorescence, we will include an inexpensive Lee Filter on the side of the holder, which we already tested several times and we know that it works. This setup allows for a filter on each side, potentially allowing for dual fluorescence measurements.

While there may still be room to optimize the cost and simplify some features, we hope this serves as a starting point at $20 per unit.
We have already placed orders for the PCBs and aluminum holders (you can find the design files here and here) and expect them to arrive in the coming weeks. Final testing and results will take a couple of months, as we try to fit it around our PhD and Master's work.
Thank you for the patience! We will keep you posted on the final results:)
2 comments