Material composition, embedding textile into the growth process and review of moulding technique
With restrictions in growing space and equipment, we are continuing our research at both a large scale (full board) and a small scale (hand board & tiles) simultaneously. The 'hand board' mould has been used to refine our material composite, our moulding methods and exploring possibilities of embedding organic textile during the growth process.
We have tested hemp husks, coffee peels and sugar cane waste as possible substrates, as well as fomes fomentarius and trametes versicolor, ganoderma lucidum and ganoderma resinaceum as mycelium strains (see previous lab notes).
Ganoderma resinaceum has showed promising results, providing a durable finish and healthy growth on all substrates, as well as performing best when submerged in water.
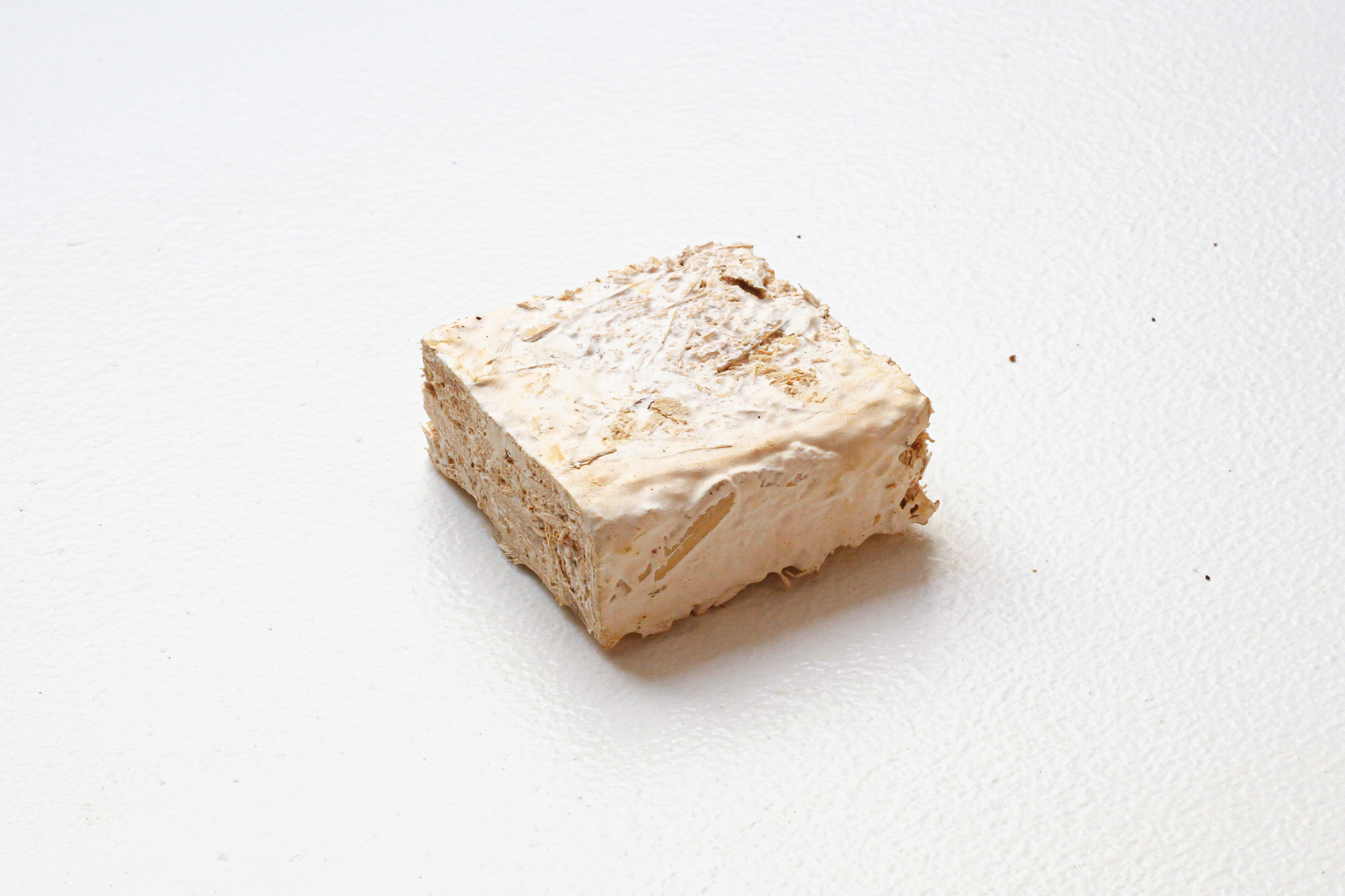
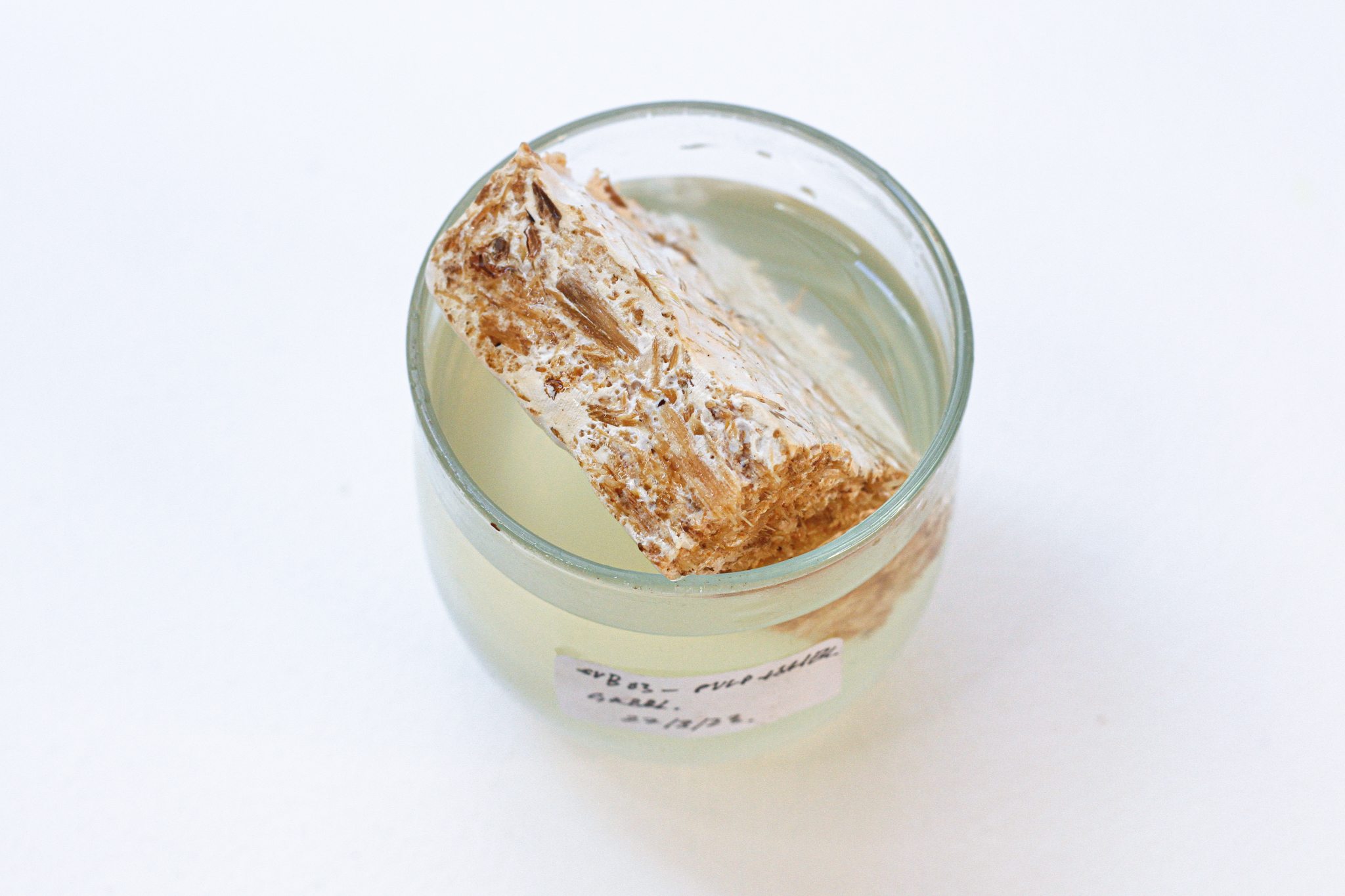
Although sugar cane waste was a good contender (lab notes pending) and performed similarly to hemp husks, obtaining and processing enough material proved challenging and energy intensive, especially given the scale at which we needed to work.
Hand moulding tests conducted:
01 - GR + hemp - 151g
02 - GR + hemp + coffee peels added during mould inoculation - 148g
03 - GR + hemp + thick cotton fabric
04 - GR + hemp + light cotton fabric - 195g
Material composition
We hypothesized that adding coffee peels to the mixture during the process of inoculating the mould would add volume without adding too much weight. This provided slightly more volume when compared to a pure hemp substrate however it left the surface of the composite more fragile and flakey and made it difficult to achieve a smooth finish without breaking when sanded.
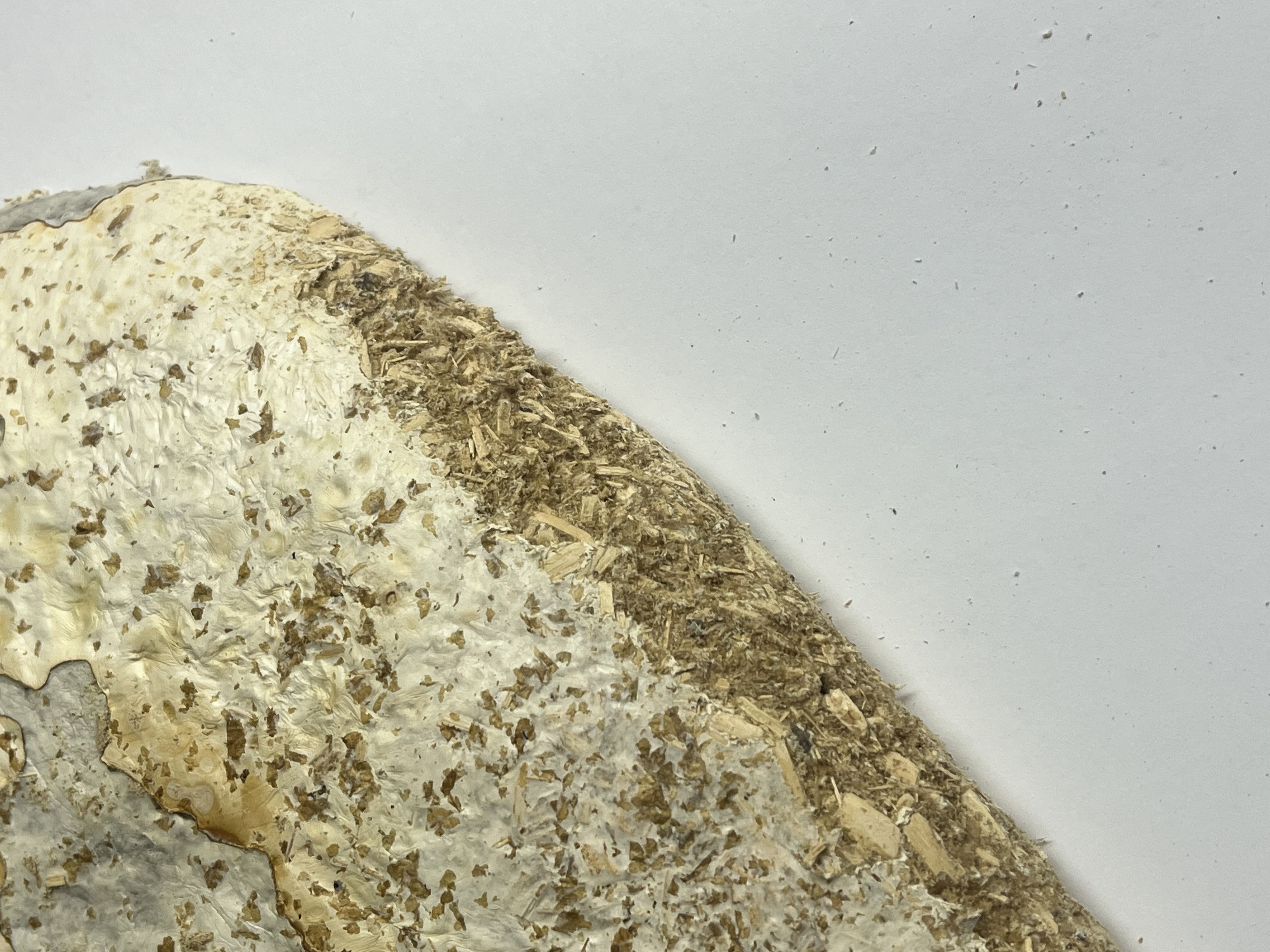
Given the ease of access and strength and performance of hemp husks in smaller tests, we decided to push forward with this as a primary substrate.
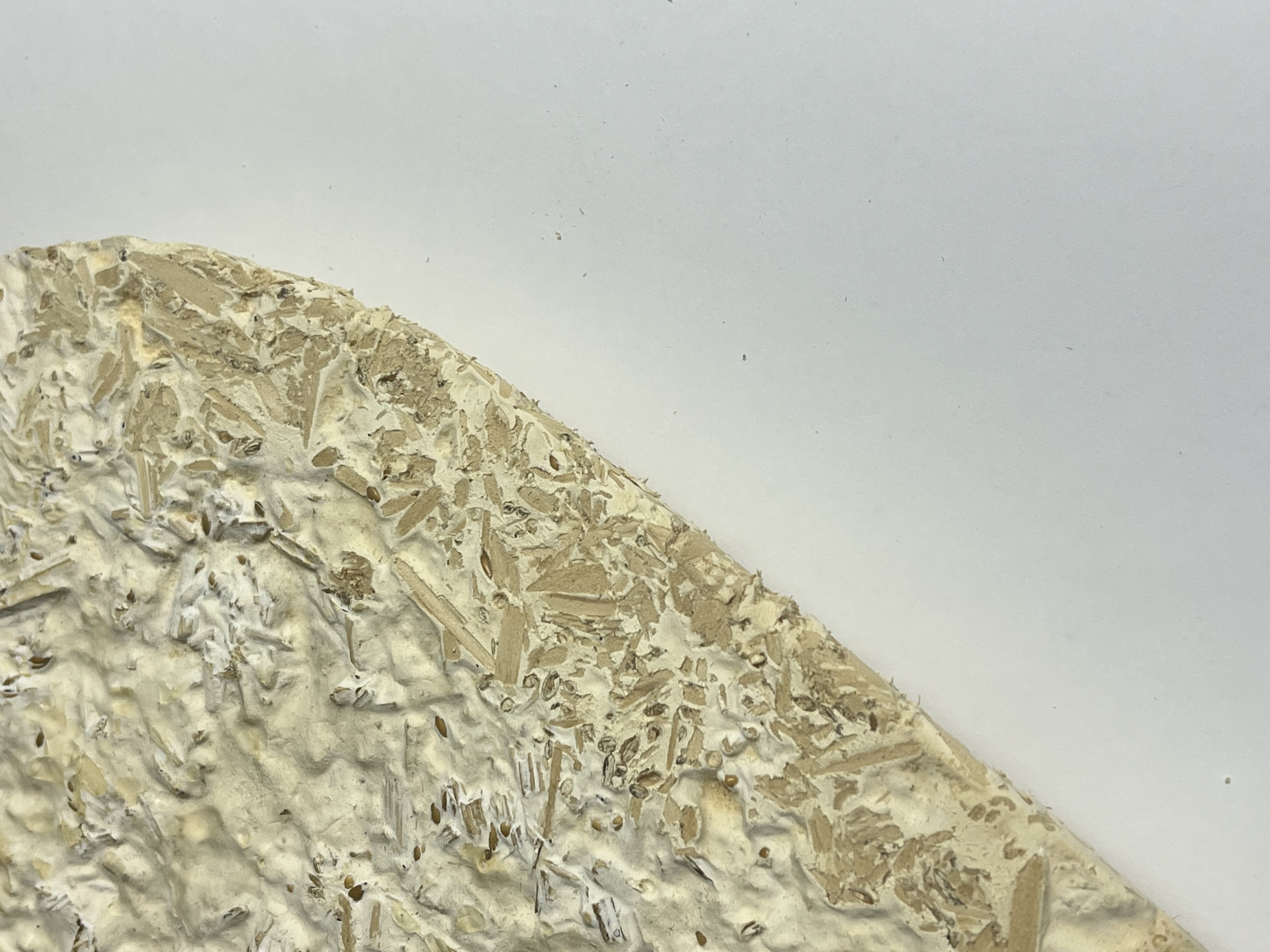
Embedding Textile
We had previously tested a thick organic cotton textile which was embedded during the inoculation of the mould; parts of the mycelium grew and covered the textile, whilst the majority was untouched.
We have now tested a thinner cotton textile with a thinner thread and larger mesh count, this proved much more promising however we still haven't achieved a smooth and consistent finish with this technique.
The added textile does provide more resistance and we will continue to explore and optimise this technique, however the disadvantage of this technique is that the composite can not be sanded once dehydrated.

Having a board with a smooth and even finish is of imperative for surfing and we are determined to achieve this by continuing to explore material composition and optimising our moulding techniques.
Ultimately our goal is to achieve a lightweight composite that provides a smooth finish once dehydrated, shaped and sanded. Whilst an embedded textile shows promising results for a smooth finish without sanding and provides added reinforcement, potentially eliminating the need for fibreglass, it does mean that the blank can not be sanded to a customised shape. More tests are needed to be done by the surf shaper in order to understand how the myco-blank would behave once the resin is applied.
Review of mould strategy
Our current technique uses a thermoformed plastic, or for the large scale, a fibreglass and resin mix provided by the surf shaper. These moulds work well as they allow us to see uniform growth, remove the composite with ease due to the flexibility of the material and we are able to provide air holes throughout.

Where the material is in contact with the mould, the finish is usually smooth. If we decide to choose a finishing strategy where shaping is omitted from the process, we will need to redesign our mould so that the material can be compressed and is in contact with both the top and bottom of the mould, similar to one of our early 3D printed moulds.
The development of this mould will be informed by the feedback given by the surf shaper.
1 comment